U 型彎折試驗機的伺服系統對測試結果有哪些影響?
點擊次數:6 更新時間:2025-07-22
控制精度決定測試參數的準確性
伺服系統的位置控制精度(通常達 ±0.01mm)直接決定彎折角度、錯動位移的設定值與實際值偏差。例如,當測試要求 180° 極限彎折時,若伺服系統定位誤差超 ±0.5°,會導致 FPC 實際彎折角度不足或過度,使線路承受的應力與預設值不符,誤判產品耐折性能。
同時,伺服系統的扭矩控制精度(誤差≤±0.1% FS)影響彎折力的穩定性。FPC 的銅箔線路、焊點在不同彎折力下的損傷閾值差異顯著,伺服系統若無法穩定輸出設定力值,會導致同一批次試樣的受力不均,測試數據離散度增大,難以準確界定產品合格閾值。

動態響應速度影響瞬態應力模擬
FPC 在電子設備中常經歷快速彎折(如手機翻蓋、智能手表表冠轉動),伺服系統的動態響應速度(響應時間≤5ms)決定能否模擬此類瞬態過程。響應滯后會導致實際彎折速度滯后于設定值,使 FPC 在 “加速 - 減速" 階段承受的沖擊應力與真實場景偏差,遺漏因瞬時過載導致的隱性斷裂風險。
例如,測試可穿戴設備 FPC 時,若伺服系統無法跟隨 100 次 / 分鐘的高頻彎折指令,會使實際彎折頻率低于設定值,導致測試周期內的總彎折次數不足,低估產品在長期高頻使用下的失效概率。

抗干擾能力保障長期測試穩定性
在持續數小時的疲勞測試中,伺服系統的抗干擾能力(如電壓波動、機械振動抑制)直接影響數據重復性。若系統受電網波動影響出現轉速波動(>±1rpm),會導致 FPC 在每一次彎折循環中的受力、角度出現細微差異,累積后使測試結果偏差超 5%,無法滿足 ISO 18070 等標準對數據重復性(誤差≤1.5%)的要求。
此外,伺服系統的閉環反饋機制(采樣頻率≥10kHz)可實時修正機械傳動誤差。當測試架因長期使用出現間隙時,系統能通過位移傳感器的實時反饋調整電機輸出,確保彎折軌跡始終貼合預設路徑,避免因機械磨損導致的測試參數漂移。
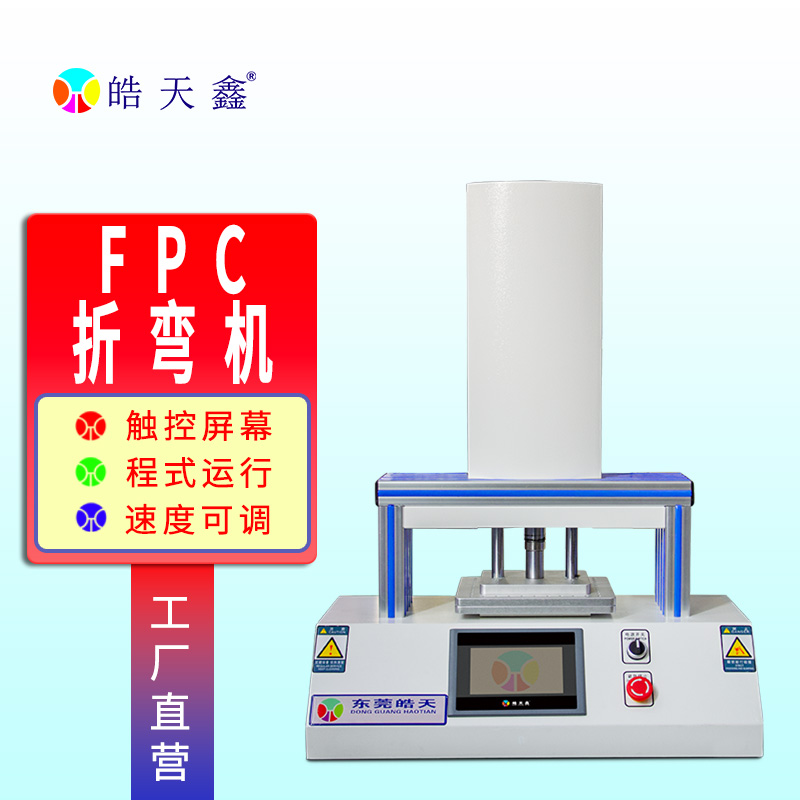
同步性控制多軸協同測試的有效性
部分 U 型彎折試驗機采用雙軸伺服系統(彎折軸 + 錯動軸),其軸間同步精度(誤差≤±0.02mm)決定復雜動作的模擬效果。例如,測試折疊屏 FPC 時,需同時實現 120° 彎折與 ±2mm 錯動,若兩軸運動不同步,會使 FPC 產生額外扭矩,導致線路斷裂位置與實際使用中的失效點不符,誤導結構優化方向。